Gasketed Heat Exchangers
Gasketed plate heat exchangers have been used for process application since the 1930's. primarily used in the dairy sector the practical advantages of this type of exchanger soon became apparent. The success of plate heat exchanger technology grew as new industrial applications were found. Modern plate heat exchangers provide a reliable and highly efficient means of heat exchange. A wide range of plate pressings and gasket arrangements are available ensuring an economical solution can be obtained. Today most process systems will include a plate heat exchanger within the design.
The gasketed family of plates offer an extremely versatile solution to plate heat exchanger requirements. All plate heat exchangers are sized utilising the latest Computer design software.
Plate Heat Exchanger selection can be classified as pressure or surface area limiting. That is the maximum allowable pressure drop has been met with a surface area greater than the calculated minimum or the design requires a minimum surface area resulting in an exchanger with a pressure drop well within specification. The best fit design is an exchanger with the maximum allowable pressure drop and minimum surface area. Most McCallum Gasketed exchangers allow for six thermal permutations from a single plate. This feature ensures McCallum exchangers offer an economic solution whose performance matches the original design criteria.
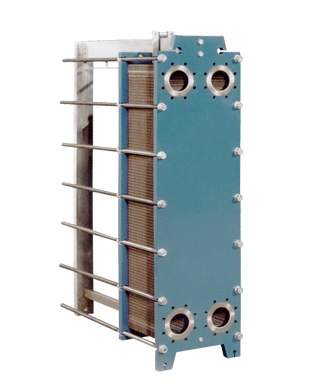